Besser, schneller und flexibler: Die semi-automatische Phased-Array-Prüfung an Radsatzkomponenten
Wartung, Instandsetzung und kontinuierliche Verbesserung sind wesentliche Werkzeuge bei der Instandhaltung von Radsatzkomponenten – wie auch die zerstörungsfreie Werkstoffprüfung. Der Einsatz der aus der Medizin bekannten Phased-Array-Technik bietet wesentliche Vorteile.
Dr. Ingo Poschmann, Geschäftsführer, W.S. Werkstoff Service GmbH
Kundenwünsche im Zentrum
Räder und Wellen sind sicherheitsrelevante Bauteile, deren hohes Sicherheitsniveau durch leistungsfähige Werkstoffe, fortgeschrittene Fertigungsverfahren, dauerfeste Auslegung und moderne Instandhaltung erreicht wird. Dazu kommt die regelmäßig durchzuführende zerstörungsfreie Werkstoffprüfung (ZfP), mit der Schäden gesucht werden, die aus unerwarteten Betriebszuständen heraus entstehen könnten.
Weiterentwicklung der bisherigen Ultraschallprüfung
Für Radsatzkomponenten ist seit Jahrzehnten die Ultraschallprüfung (UT) als Prüfverfahren etabliert. Innerhalb dieses Prüfverfahrens wurde in den letzten Jahren die bereits aus der Medizin bekannte Phased-Array-Technik (PAUT) kontinuierlich weiterentwickelt. Sie verbindet hohe Zuverlässigkeit mit kurzen Inspektionszeiten.
Das Bild 1 zeigt ein mobiles, PAUT-basiertes Scansystem für Radsätze. Die PAUT-Technik ist eine bildgebende Technik: Signale, die durch einen Fehler oder durch die Geometrie erzeugt werden, werden als farbige Anzeigen mit direktem Bezug zur Bauteilgeometrie dargestellt. Das ist nützlich, wenn vorab Zeichnungen in das Prüfgerät importiert und die Konturen des Bauteils zusammen mit den PAUT-Signalen während der Prüfung gegenübergestellt werden. Das wird im Bild 2 deutlich. Der Abgleich der Anzeigen der inneren und der äußeren Radsitzkante mit der Wellenkontur erlaubt eine rasche Orientierung für das Prüfpersonal und eine Zwischenkontrolle der Prüfergebnisse.
Der Prüfbereich ist in diesem Beispiel der Pressverband Rad-Welle – also die Verbindungslinie zwischen beiden Radsitzkanten. Alle PAUT-Signale, die auf dieser Linie sichtbar werden, weisen auf Risse hin. Diese bildgebende Signaldarstellung unterstützt den Prüfer erheblich und erleichtert den Fehlernachweis.
Zu den Vorteilen eines solchen Prüfsystems gehören:
- Modularer Aufbau: Mit einer einzigen Hard- und Softwarebasis können unterschiedliche Prüfkonzepte realisiert werden – von der mobilen Handprüfung bis hin zu Prüfständen mit mehreren simultan arbeitenden Sensoren.
- Verkürzung der Inspektionszeiten: Der exzellente Fehlernachweis geht einher mit einer deutlichen Verkürzung der Prüfzeiten im Vergleich zur konventionellen Handprüfung. Ein einziger Scan mit PAUT kann viele konventionelle Prüfvorgänge ersetzen.
- Automatisierte Berichterstellung: Die Software moderner PAUT-Systeme gestattet es, individuelle und papierlose Prüfberichte automatisiert zu erstellen.
- Rohdaten-Erfassung und -Speicherung: Da die PAUT-Prüfköpfe zusammen mit Wegaufnehmern betrieben werden, können sämtliche Prüfdaten ortsgenau erfasst und gespeichert werden.
- Trennung von Prüfung und Bewertung: Wenn Rohdaten erfasst werden und die korrekte Ankoppelung der Prüfköpfe nachgewiesen ist, dann können Prüfung und Bewertung zeitlich getrennt werden. Das gestattet es, die Effektivität und Flexibilität der Prüfprozesse zu erhöhen.
- Erhöhung der POD: Die Hard- und Software der PAUT-Systeme erlaubt es, die Fehler-Nachweiswahrscheinlichkeit (POD) deutlich gegenüber konventionellen UT-Prüfsystemen zu erhöhen.
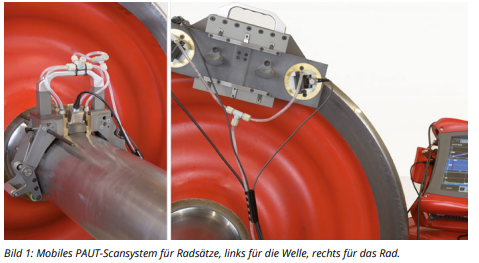
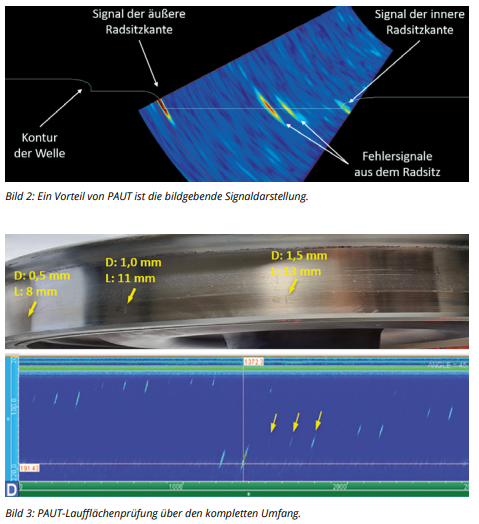
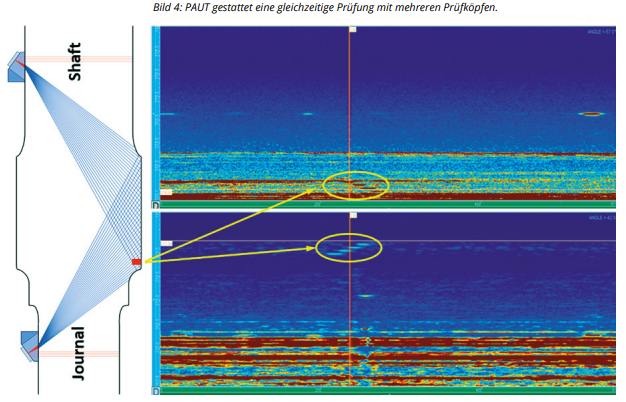
Volle Stärke bei Kopplung mit Wegaufnehmern
PAUT-Systeme zeigen ihre Stärken vor allem dann, wenn sie mit Wegaufnehmern gekoppelt werden. Bild 3 zeigt ein Referenzrad mit künstlichen Fehlern unterschiedlicher Tiefe (D) und Länge (L). Diese Fehler sind in Gruppen über die Lauffläche und den Umfang des Rades verteilt. Der PAUT-Prüfkopf (nicht im Bild) befindet sich auf der inneren Stirnfläche des Rades. Unten im Bild 3 ist der aufgezeichnete Scan zu sehen, der die gesamte Lauffläche über den gesamten Umfang abdeckt. Alle künstlichen Fehler werden – trotz zum Teil sehr geringer Größe – mit einem einzigen Scan von etwa einer Minute gefunden. Darüber hinaus gestattet dieser Scan, die Länge und Tiefe künstlicher Fehler anhand der Anzeigenlänge und der farbkodierten Signalhöhe abzuschätzen.
Bild 4 zeigt ein Setup für die Prüfung des Pressverbandes mit zwei Prüfköpfen, die gleichzeitig arbeiten. Eine Phalanx aus mehreren Reflektoren befindet sich ganz in der Nähe der äußeren Radsitzkante. Der auf dem Schaft positionierte Prüfkopf erkennt diese Reflektoren nur schwach. Der Grund: Diese Reflektoren werden vom Echo der äußeren Radsitzkante nahezu „überstrahlt“. Für den Prüfkopf auf dem Schenkel ist die äußere Radsitzecke dagegen praktisch kein Reflektor. Die Phalanx lässt sich daher sehr gut erkennen.
Mehrere Prüfköpfe maximieren Informationsgewinn
Der Vorteil der Prüfung mit zwei gleichzeitig arbeitenden Prüfköpfen liegt auf der Hand: Beide Sonden unterstützen und bestätigen sich permanent gegenseitig. Auf diese Weise erhält man maximale Informationen und verbessert die POD erheblich.
Unser Fazit: Prüfungen mit Phased-Array-Ultraschall bieten Anwendern maximale Sicherheit – bei hoher Prüfgeschwindigkeit, vollem Zugriff auf belastbare Prüfdaten und flexiblem Einsatz der Prüfsysteme.